MOULD REMEDIATION
At North Queensland Flood Restorations, we specialise in detailed water damage inspections, Structural Drying and Mould remediation in Cairns
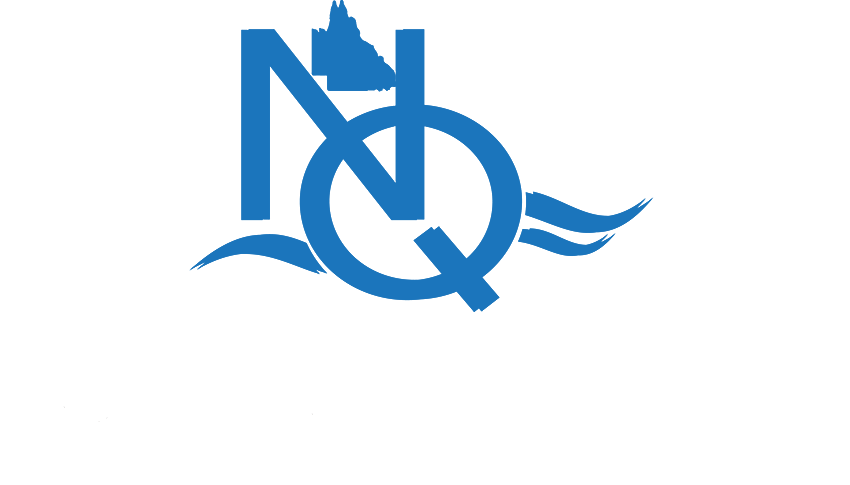
MOULD
Mould Remediation Cairns
NQFR specialise in Mould Remediation.
Our mould inspections start with identifying the affected areas and determining the cause of the growth. We take into account the Atmospheric conditions, ventilation and moisture content of the affected materials. We then prepare a site specific remediation process plan how to best treat the area. Depending on the extent of the damage removal and disposal of the materials maybe required.
If required and requested mould samples are taken and sent for laboratory testing identifying the mould species and concentrations. A detailed report is prepared with the independent laboratories findings.
Understanding Mould
Microscopic mould spores exist almost everywhere, outdoors and indoors, making it impossible to remove all mould from a home or business. Some restoration businesses advertise “mould removal” and even guarantee to remove all mould, which is a fallacy.
Mould spores are present almost everywhere
Mould spores are microscopic and float along in the air, and may enter your home through windows, doors, or AC/heating systems or even hitch a ride indoors on your clothing or on a pet. Mould spores thrive on moisture and can quickly grow into colonies when exposed to water.
Mould often produces a strong, musty odour.
and can lead you to possible mould problem areas. Even higher-than-normal indoor humidity can support mould growth. Keep indoor Relative humidity below 60 percent.
Mould Decontamination Process
Step 1: Contact
The mould clean up and restoration process begins when you call. Our representative will ask a series of questions to help us determine the necessary equipment, resources, and personnel required. From residential or commercial, rental or private our services are tailored to each scenario.
Step 2: Inspection and Mould Damage Assessment
We will carefully inspect your property for visible signs of mould. Mould feeds on dead organic material and can be hidden from plain view. We use various technologies to detect mould and hidden water sources including the use of a highly sensitive Infrared camera operated by a certified Level II Thermographer, Moisture detection equipment and taking Bio tape samples for laboratory testing.
Step 3: Identify and address the source of the water ingress
We conduct a site inspection to determine the source of the potential water intrusion and take measures to stop the ingress.
Step 4: Mould Containment
We use various containment procedures to prevent the spread of mould. We may use advanced containment procedures like negative air chambers to isolate the contaminated area with physical barriers and negative air pressure to keep the mould spores from spreading during the clean-up process. All fans and heating and cooling systems will be turned off to prevent the spread of mould.
Step 5: HEPA Air Filtration
Our specialised filtration equipment allows us to capture microscopic mould spores out of the air. We utilise powerful “Air Scrubbers” and HEPA vacuums to prevent the spread of these mould spores while the mould remediation is in process.
Step 6: Removing Mould and Mould-Infested Materials
The mould remediation process depends on the amount of mould growth and the types of surfaces on which the mould appears. When the mould affected building material cannot be physically removed we use a combination of antifungal, antimicrobial treatments to eliminate mould colonies and to help prevent new colonies from forming. ULV Fogging and Ozone equipment is used to combat odour problems. In some cases, removing and disposing of mould-infested porous materials, like plaster and carpeting, may be necessary to remediate heavy mould growth.
Step 7: Environment Modification and structural Drying
It is critical to modify the affected environment removing the source of the elevated moisture and conducting structural drying and dehumidification. This will ensure the habitat mould requires to thrive is eliminated decreasing the chance of it re developing.
Step 8: Thermal/ULV fogging and Ozone for odour Control
The deodorization process consists of using a Thermal/ULV Fogger and Ozone equipment to remove any air born odours.
Step 9: Final Inspection
We conduct a Thermal Scan and Moisture test the treated areas ensuring they are dry. If requested a final Bio tape swab test can be taken and sent for independent laboratory testing.
Step 10: Restoration Building Repairs
Depending on the level of mould damage, plaster, sub-floors, and other building materials may be removed and replaced. Restoration may involve minor repairs, such as replacing plaster board, painting, and installing new carpet; or it may entail major repairs such as the reconstruction of various areas or rooms in a home or business. As a Licensed Builder we can assist you in these repairs.
WE ARE AVAILABLE 24 HRS A DAY - 7 DAYS A WEEK
CALL US ANYTIME. NO JOB IS TOO BIG OR TOO SMALL
CALL 1300 628 600
RECENT WORK
What We Do
- 24/7 Emergency Water Extraction
- Structural Drying
- Decontamination / sanitization of buildings
- HEPA Air filtration
- Mould remediation & laboratory testing
- Odour control & deodorisation
- Ozone treatments / ULV Fogging
-
Infrared thermal imaging
- Non invasive leak detections of wet areas
-
Specialised thermographic building investigations
- Emergency restoration make safes
- Building insurance assessments
- Forensic water intrusion
- Thermal imagery of water damages
- Moisture ingress investigations